Component Failure Analysis
Methodology
Our systematic analysis of a failed part begins with visual and low power microscopic inspection. Depending on the initial inspection results, we may use higher power optical magnification, SEM (Scanning Electron Microscopy), EDS (Energy Dispersive Spectroscopy), penetrant testing, hardness testing, and micro-hardness testing. The results of these tests may lead into additional destructive testing including metallography analysis, and if the part is large enough or additional material is available, tensile or impact testing.
Our analysis goes beyond typical failure analysis to include vibration analysis, repair procedures, maintenance history, and operating data to discover failure modes and contributing factors.
We are able to collect and interpret vibration data for EMA (Experimental Modal Analysis), ODS / Motion Amplification (Operating Deflection Shape) analysis, shaft orbits, vibration spectra, and run up / coast down testing.
Years of experience in equipment reliability gives us the unique ability to review repair history, maintenance procedures and operating data to discover hidden roots of a failure.
Our analysis will tell you what needs to be done to prevent another failure.
Our Analytical Equipment
- Rockwell hardness
- Brinell hardness
- Leeb hardness
- Vickers micro hardness
- Tensile strength
- Charpy impact
- Fatigue strength
- Optical Microscopy
- Energy Dispersive Spectroscopy
- Optical Emission Spectroscopy
- Scanning Electron Microscopy
- Metallographic sectioning and polishing
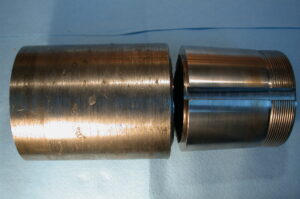
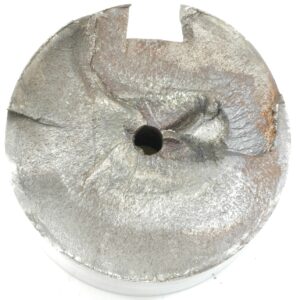
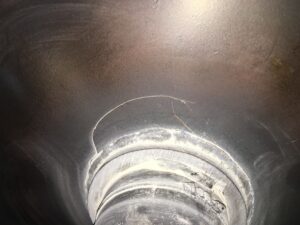
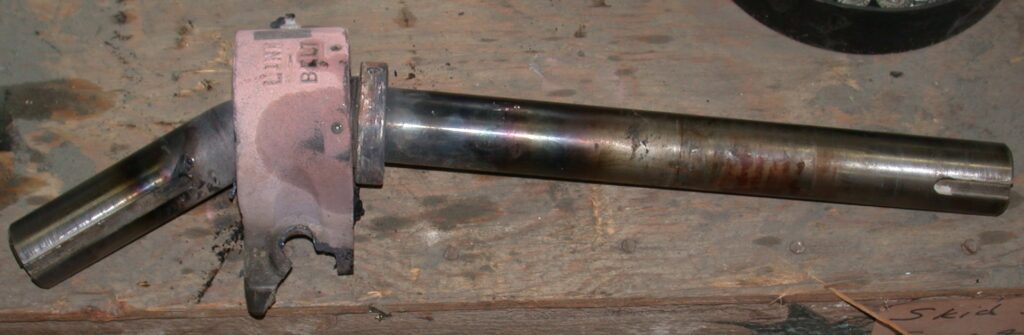