Vibration Analysis
Torsional vibration analysis & modeling
Torsional vibration can be an unseen killer of equipment. Often the only indication of a torsional problem is repeated failures of shafts, gears or couplings.
Torsional fatigue failures have been associated with internal combustion engines, marine drives and long slender equipment configurations. But, with the increased use of variable frequency drives to optimize efficiency, high vibration may occur at certain speeds in equipment not typically associated with torsional vibration.
Alignment checks, bump tests, and vibration data don’t show any abnormaladies. Construction of a torsional model and torsional measurements will uncover problems that may be readily corrected.
Operating Deflection Shape Analysis / Motion Amplification
Frequently it is very difficult to visualize how a machine is vibrating while running.
An Operating Deflection Shape (ODS) analysis produces visual animations of a machine’s response at a specific frequency or time interval while it is running. An Operating Deflection Shape (ODS) analysis uses vibration data to animate a computer model.
These animations allow observation and intuitive analysis of complex vibration data. Then effective solutions to complex vibration problems become possible.
Modal Analysis
Every machine has natural frequencies.
When a natural frequency conicides with a frequency caused by the operation of a machine, the resulting vibration is amplified. This is called resonance. It frequently causes fatigue failure.
Modal analysis will identify the natural frequencies and the way in which the machine or structure moves or vibrates at each natural frequency in a computer model.
Then, steps can be taken to change the natural frequency by changing mass, stiffness, and / or damping. Modifications can be tested using the computer model for effectiveness before changing the machine or structure.
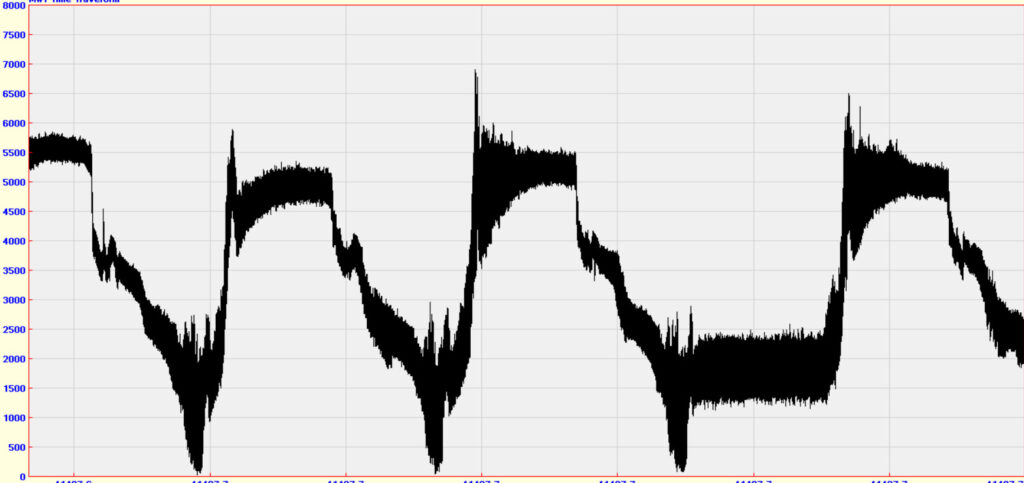